Plastic extrusion for creating standardized, premium parts
Plastic extrusion for creating standardized, premium parts
Blog Article
Comprehending the Essentials and Applications of Plastic Extrusion in Modern Manufacturing
In the world of modern production, the strategy of plastic extrusion plays an important duty - plastic extrusion. This complex process, entailing the melting and shaping of plastic with specialized passes away, is leveraged across various markets for the development of diverse items. From car components to durable goods packaging, the applications are huge, and the capacity for sustainability is just as impressive. Unraveling the basics of this procedure reveals truth flexibility and capacity of plastic extrusion.
The Basics of Plastic Extrusion Refine
While it may show up complex, the principles of the plastic extrusion procedure are based on relatively uncomplicated concepts. It is a manufacturing process wherein plastic is thawed and after that shaped into a constant profile through a die. The plastic extrusion process is thoroughly used in numerous industries due to its versatility, efficiency, and cost-effectiveness.
Various Kinds Of Plastic Extrusion Techniques
Building upon the standard understanding of the plastic extrusion process, it is needed to check out the different techniques associated with this production technique. Both primary strategies are profile extrusion and sheet extrusion. In account extrusion, plastic is melted and formed into a constant account, typically used to develop pipes, rods, rails, and home window frames. On the other hand, sheet extrusion develops large, flat sheets of plastic, which are generally more refined into products such as food packaging, shower curtains, and cars and truck components. Each technique needs specialized equipment and precise control over temperature level and stress to make sure the plastic maintains its shape throughout cooling. Understanding these methods is vital to making use of plastic extrusion efficiently in modern manufacturing.
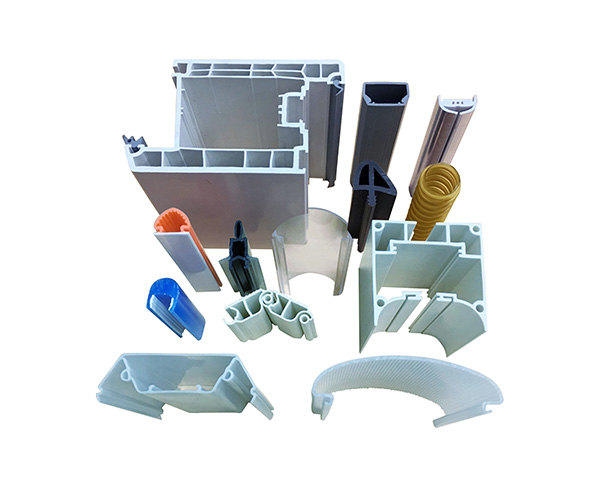
The Duty of Plastic Extrusion in the Automotive Market
An overwhelming majority of components in modern-day cars are products of the plastic extrusion procedure. Plastic extrusion is primarily utilized in the production of various auto parts such as bumpers, grills, door panels, and dashboard trim. Therefore, plastic extrusion plays an essential role in vehicle manufacturing.

Applications of Plastic Extrusion in Durable Goods Production
Beyond its considerable influence on the auto industry, plastic extrusion confirms similarly effective in the world of redirected here consumer goods manufacturing. This procedure is critical in producing a broad selection of products, from food packaging to household devices, toys, and even clinical gadgets. The convenience of plastic extrusion enables manufacturers to make and produce complicated sizes and shapes with high precision and efficiency. Due to the recyclability of numerous plastics, squeezed out components can be reprocessed, lowering waste and expense (plastic extrusion). The flexibility, versatility, and cost-effectiveness of plastic extrusion make it a recommended option for many consumer items manufacturers, adding considerably to the market's growth and innovation. Nevertheless, the environmental ramifications of this extensive usage need cautious consideration, a topic to be reviewed further in the succeeding area.
Environmental Effect and Sustainability in Plastic Extrusion
The prevalent use of plastic extrusion in producing invites analysis of its environmental ramifications. Efficient machinery lowers power use, while waste monitoring systems recycle scrap plastic, decreasing raw product needs. Regardless of these improvements, better advancement is needed to minimize the environmental footprint of plastic extrusion.
Conclusion
To conclude, plastic extrusion plays an essential function in modern-day manufacturing, particularly in the vehicle and durable goods sectors. Its versatility enables for the production of a vast array of components with high precision. Moreover, its capacity for recycling and development of eco-friendly materials offers an appealing method towards sustainable techniques, thereby resolving environmental problems. Recognizing the essentials of this process is vital to maximizing its advantages and applications.
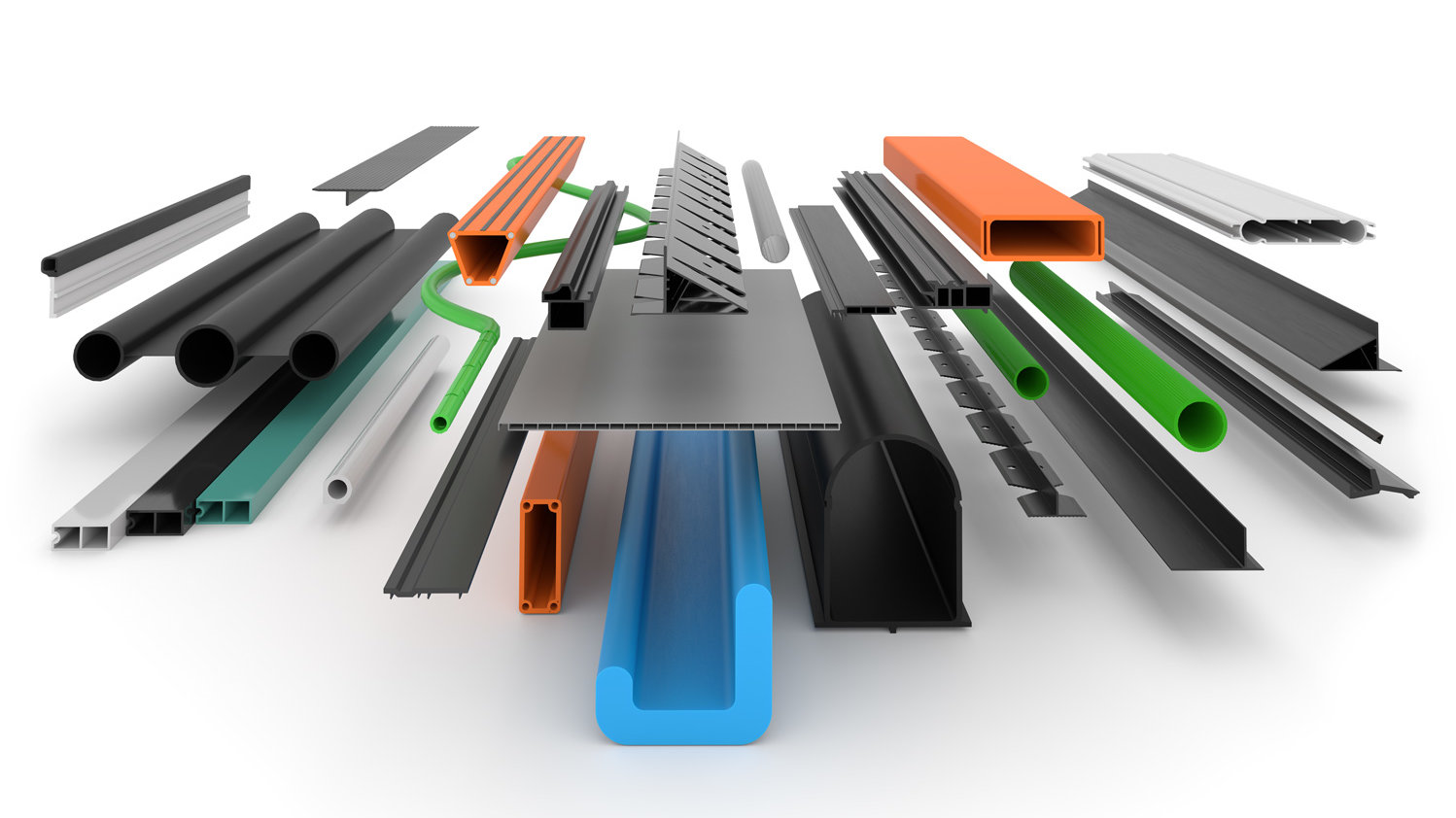
The plastic extrusion process is extensively made use of in numerous markets due to its versatility, performance, and cost-effectiveness.
Structure upon the fundamental understanding of the plastic extrusion process, it is necessary to discover the different methods included in this manufacturing method. plastic extrusion. In comparison, sheet extrusion produces large, level sheets of plastic, which are typically more processed into items such as food packaging, shower curtains, and auto components.A frustrating majority of parts in modern-day lorries are products of the plastic extrusion procedure
Report this page